HM Superfine Ring Roller Mill
We offer complete industry grinding mill production line for designs, installation, support and maintenance with long-term technical support and fast response.
HM Superfine Ring Roller Mill
DEVICE DETAILS:
Economical and practical ultrafine powder processing equipment
HM ultrafine ring roller mill is a new type of ultrafine power processing equipment. The product powder fineness can be adjusted between 325 mesh and 2500 mesh according to the needs, fineness can reach D97≤5um. This machine has comprehensive mechanical grinding performance such as rolling, grinding, impact, etc.. It has advantages of small footprint, strong completeness, wide application, simple operation, convenient maintenance, stable performance, cost-effective, and energy-saving. It is suitable for deep processing of non-metallic minerals, talc, calcite, calcium carbonate, dolomite, potassium feldspar, bentonite, kaolin, graphite, carbon and other non-metallic materials with Mohs hardness of 7 or less and humidity within 6%.
Finished particle size: 5-45μm
Production capacity: 1-22t / h
ADVANTAGE
1. Reliable Performance
Higher production capacity and lower power consumption: Non metallic mineral particles feed which feeding size is less than 10mm, can be one-time processed as < 10 m powder (97% passing). The particle size less than 3um accounted for about 40%,which contributes to a larger specific surface area. It has the advantages of low cost, high efficiency, and good product fineness.
2. Forced Turbine Classifying System
Wide fineness and flexible adjustment: Turbine classifier (patent no.: ZL201030143470.6). The fineness can be adjusted flexibly from 0.04mm (400 mesh) to 0.005mm (2500 mesh). Products with various fineness can meet the market needs and improve your competitiveness.
3. Environment-friendly: Full Pulse Collecting System
Environmental protection: The pulse collecting system will remove 99.9% of the dust, ensuring dust-free operation environment. The pulse dust collection system is Hongcheng special invent comply for the environment protection requirements.
Thorough Cleaning:The pulse dust collection system is adopted with pulse-jet type of cleaning. By utilize the compression air to shoot clean each filtering bag. High and complete dust cleaning. Prevent bags from powder stocking.
4. Lower Wear-resistance Rate
The wearing parts(roller and ring) made from special wear-resistant material which prolongs working life.
5. Absorb Vibration and Compact Structure, high safety and reliability
The mill base is inblock casting, which ensures the structural strength and alleviates vibration.
TECHNICAL PARAMETERS:
Model | Roller Number | Ring Number | MaxFeeding size(mm) | Fineness(mm) | TotalPower(kw) | Classifier Power (KW) | Fan Power (KW) |
HM780 | 17 | 2 | ≤10 | 0.04-0.005 | 75 | 22 | 37 |
HM980 | 28 | 2 | ≤10 | 0.04-0.005 | 132 | 30 | 75 |
HM1395 | 36 | 2 | ≤10 | 0.04-0.005 | 200 | 75 | 160 |
CASE:
HM Ultrafine Mill – 60,000t/year coarse whiting micro powder project in Hunan China
The running project owner is a long term customer of Guilin HM Machinery. The customer owned the calcite mine, majority process coarse whiting fine powder. The customer’s site has 1 set of HM1300 Grinding Mill for 400 mesh D97 coarse powder producing, 1 set of HM980 and 1 set of HM1395 Ultra-fine Mill for 800-1500 mesh D97 powder.
Production Status
Material: Coarse Whiting Powder
Product Fineness: 1250 Mesh, D97
Capacity: HM1395: 5.5-6 TPH, HM980: 2.5-3 TPH
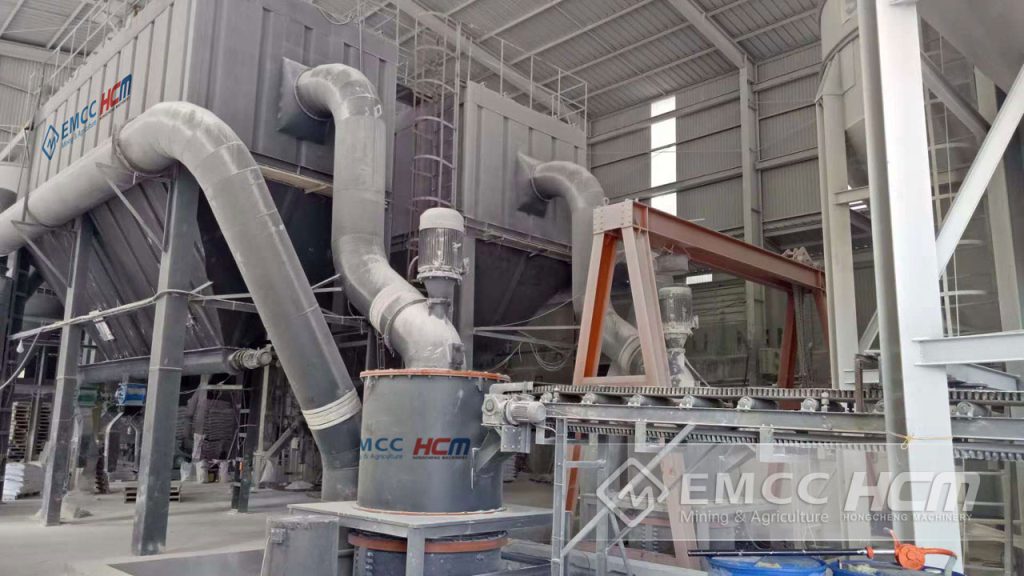
HM Ultra-fine Mills – 120,000t/year coarse whiting ultra-fine powder project in Guangdong China
The customer is a famous enterprise in coarse whiting industry. The project is for new constructed workshop. The customer has high requirement of environmental performance, capacity and energy cost. After several investments and comparisons, the customer finally selected 2 sets of HM1395 Ultra-fine Mills. The Grinding Mills start operation in 2014.
Production Status
Material: coarse whiting
Product fineness: 1250 mesh D97
Capacity: 5.5-6t/h
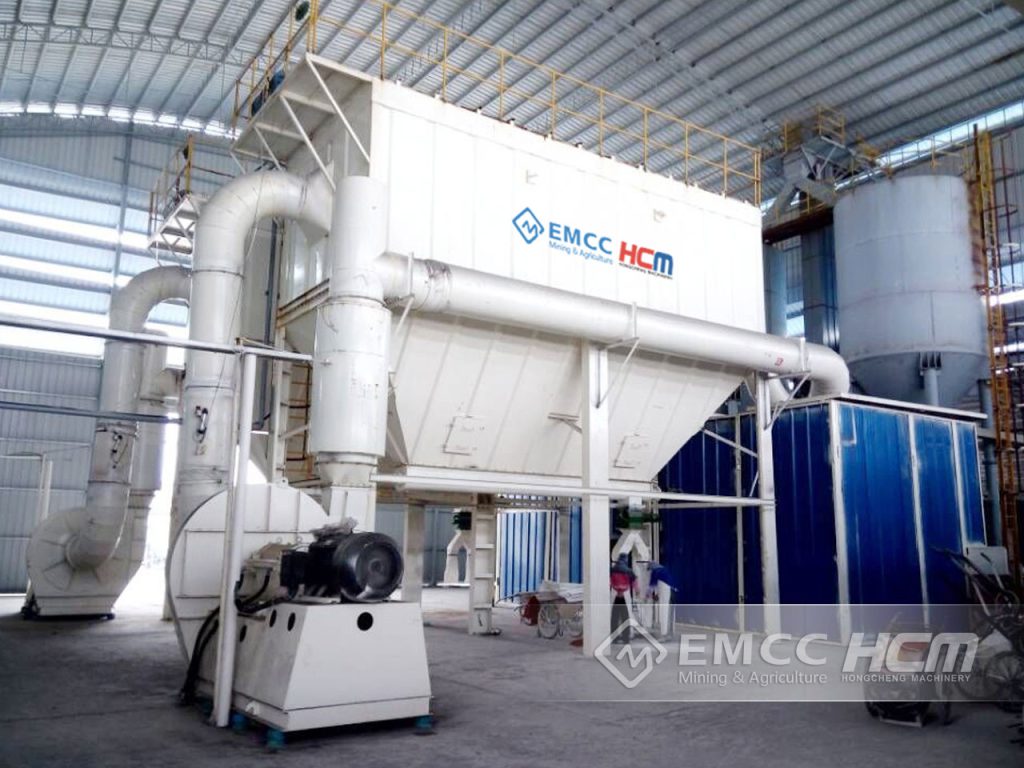
WORK PRINCIPLE:
Technological process: The pre-grinding raw ore material will be crushed into particles<10mm and transport to the feeding hopper by the elevator, then feed into the grinding chamber by the feeder. The grinding rollers equip on the rotary table rotates around the centre shaft. There is flexible gap between the roller and ring. The rollers rotate outward by the centrifugal function to compress the fixed ring. The rollers also self- rotates around the roller pin. When material passed through the gap between the ring and roller, the material will be smashed by the rotating rollers. Four layers of rollers. Material will be grinded 1st time when passing the 1st layer of roller and ring. Then be grinded second, third and fourth time when loop through each layer rollers. Thus the materials were grinded sufficient and obtain much fine powder. The powder fallen down onto the bottom table by gravity will goes up to the classifier for separation by the airflow from blower. The qualified fineness passing from the classifier will be collected by the pulse bag collector as final product, while unqualified fallen down for regrinding till passing through. The powder goes with air flow into the pulse bag filter and collects by the discharging valve. The wind path is in circulation and the airflow is in negative pressure. There will be no dust escape, so the equipment can ensure a no dust operation in workshop.
Application Range
HM Ultra-fine Grinding Mill is widely used to grind any non-metallic minerals with Moh’s hardness below 7 and moisture below 6%, such as talc, calcite, calcium carbonate, dolomite, bentonite, kaolin, graphite, carbon black etc.. This kind of mill is especially suitable for ultra fine grinding. The fineness can be adjusted from 0.045mm(325 mesh) to 0.005mm(2500 mesh), whose range is much wider than that of traditional Raymond Mill.
VIDEOS More