RM Series Pendulum Mill
We offer complete industry grinding mill production line for designs, installation, support and maintenance with long-term technical support and fast response.
RM Series Pendulum Mill
DEVICE DETAILS:
Raymond mill also called as pendulum mill
After more than one hundred years of practice and continuous innovation and improvement, the RM Raymond mill (pendulum mill) has been perfected in structure. EMCC has adopted advanced new technology to upgrade various technical indicators, which is the weathervane of domestic Raymond mill technology innovation.
TECHNICAL PARAMETERS:
Model |
RollerAmount |
Ring Number |
MaxFeeding size(mm) |
Fineness(mm) |
Mainframe power (KW) |
Classifier Power (KW) |
Fan Power (KW) |
RM110-3 |
3 |
1 |
≤15 |
0.18-0.038 |
45 |
11 |
45 |
RM110-4 |
4 |
1 |
≤25 |
0.18-0.038 |
45 |
11 |
45 |
RM130-4 |
4 |
1 |
≤25 |
0.18-0.038 |
75 |
15 |
75 |
RM160-4 |
4 |
1 |
≤25 |
0.18-0.038 |
132 |
18.5 |
132 |
RM170-4 |
4 |
1 |
≤30 |
0.18-0.038 |
160 |
22 |
160 |
RM180-4 |
4 |
1 |
≤40 |
0.18-0.038 |
160 |
22 |
160 |
RM190-5 |
5 |
1 |
≤40 |
0.18-0.038 |
160 |
22 |
160 |
ADVANTAGE:
1. The grinding mill is in stereo-chemical structure, consume small floor space. The equipment has strong systematic because it can organize an independent and complete production system of raw material crushing, transporting, grinding to production collecting, storing and packing.
2. Driving system (double gearing, single gearing and reducer) and classify system (classifier and analyzer) can be configured according to the material or customer requirement, in order to ensure best operation condition.
3. Depending on the material to configure the pipe and blower system, in order to reduce wind resistance and pipe abrasion, ensuring high capacity.
4. Applied high quality thicken steel to produce important parts, applied high performance wear-resistant material to produce wear-resistant parts. The equipment has high wear-resisting property and reliable operation.
5. Centralized controlled electric system realized unmanned operation and easy maintenance.
6. Pulse exhaust system can be applied to deal with remain air. Filtering efficiency can reach 99.9%.
WORK PRINCIPLE:
Raw material is firstly broken by jaw crusher into required particle size, which are carried by bucket elevator up to the storage hopper. The vibration feeder then conveys the crushed materials at a fixed rate into the grinding chamber of the main unit for pulverizing.
The three rollers hung upon the spider-arm are running around the shaft. With the centrifugal force, the four rotational rollers will go around the ring tightly. The raw materials is put up between the rollers and rings by the blade to make the raw materials into powder. The grinded materials is blown up to the classifier, through which the powder is separated by the airflow.
Coarse particles fall back down to the mill for regrinding.
The needed particles will go into the collector where products will be removed through the discharge opening. The purified air flows to the air blower through the pipe above big cyclone collector. Air flue is circular type. Air stream in all pipelines is negative pressure except for that in the air blower and grinding chamber, which improved the working condition in the workshop.
Wind volume in air flue increases as the moisture in material changes into vapour leaking in from the flange conjunctions and feed opening. Added air volume is transporting through the air blower and after-wind pipe, to simple collector. The end powder enters the collector with air stream and discharged from discharge valve.
Application Range
RM-series Grinding Mill is widely used to grind any non-metallic minerals with Mohs hardness below 7 and moisture below 6%, such as limestone, calcite, activated carbon, talc, dolomite, titanium dioxide, quartz, bauxite, marble, feldspar, barite, fluorite, gypsum, ilmenite, phosphorite, clay, graphite, kaolin, diabase, gangue, wollastonite, quick lime, silicon carbide,bentonite, manganese.
The fineness can be adjusted from 0.18mm(80 mesh) to 0.038mm(400 mesh), whose range is much wider than that of traditional raymond mill.
MILL STRUCTURE:
RM-Series Roller Mill consists of main mill, electromagnetic-vibrating feeder, constraint turbine classifier, pipes, high pressure blower, cyclone separator, hopper, electronic control system, collecting system, jaw crusher, pan elevator, base, central shaft support, ring, spider-arm, roller assembly, shaft, lifter support, lifter support base etc.
The main mill consists pedestal, return air box, shovel, roller, ring, housing and motor. The ring and roller are made from wear-resistant material, whose surface is also given wear-resistant treatment. For the driving system, there are reducer and double-motor system for option. The classifying system uses the turbine classifier.
Various feeding and conveying system can be done separately according to different material. The close system with cyclone plus pulse-jet collector and the open system with only pulse-jet collector are available for collecting system. As to the control system, you can select auto control or remote control.
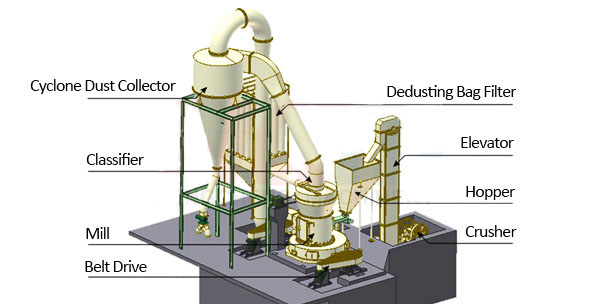
VIDEOS More